In mijn vorige artikel heb ik uitgelegd hoe je in PROPOS eenvoudig WIP analyses maakt en hoe je daarmee bottlenecks binnen je productieproces identificeert om richting te geven aan verbeterprojecten. In dat artikel stip ik een aantal onderwerpen aan voor toekomstige artikelen. Eén daarvan is de analyse leveringsbetrouwbaarheid per productiecel (lees: afdeling). In dit artikel zal ik daar dieper op ingaan. Maar laat ik eerst PROPOS nog kort neerzetten om dit artikel in de juiste context te plaatsen.
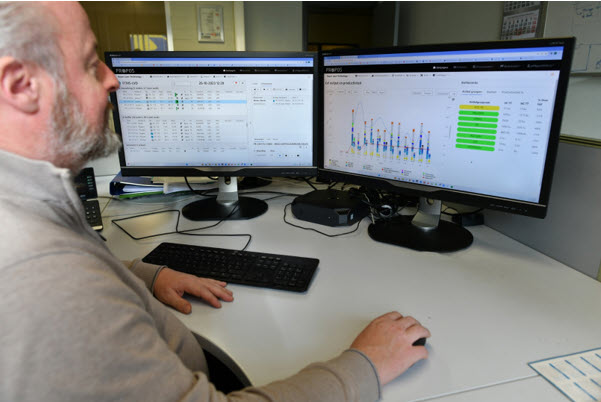
“Productieleiders kunnen via het dashboard in één oogopslag zien welke onderdelen van productie aandacht nodig hebben en waar alles goed gaat.”
PROPOS software is een oplossing voor productieplanning, werkvloeraansturing en procesoptimalisatie, gericht op productiebedrijven met veel variatie. Met veel variatie bedoelen we veel verschillende klantordergestuurde artikelen, grote en kleine orders door elkaar, complexe en eenvoudig producten door elkaar. Voorcalculatie is niet altijd gemakkelijk en daardoor niet altijd nauwkeurig. Er is een grote afhankelijkheid van de beschikbaarheid van (bepaalde) mensen en machines. Door die grote mate van variatie is plannen op de traditionele manier erg moeilijk, net zoals het bewaren van overzicht van alles dat op de werkvloer gebeurt. PROPOS – gebaseerd op de principes van Quick Response Manufacturing (QRM) – biedt een oplossing om sneller, vaker op tijd en met minder moeite (overhead) te produceren. Onze klanten zijn bijvoorbeeld productiebedrijven in de metaal-, hout- en kunststofsector. Denk aan plaatverwerkers, verspanende bedrijven, interieurbouwers, meubelbedrijven, enzovoort.
Eenvoudig gezegd werkt PROPOS op drie niveaus. Ten eerste real time op de werkvloer zelf. Ten tweede op kantoor bij productieleiding, verkoop en planning waar ook real time informatie alsmede (middel)lange termijn informatie beschikbaar is. En ten derde voor de mensen die met (lange termijn) verbeterprojecten bezig zijn. Voor die mensen biedt PROPOS een gebruikersvriendelijke analysemodule die allerlei inzichten geeft op het gebied van bottlenecks, leveringsbetrouwbaarheid en voor-/nacalculatie. Van die analysemodule zal ik in dit artikel de analyse ‘cel -OTD’ behandelen.
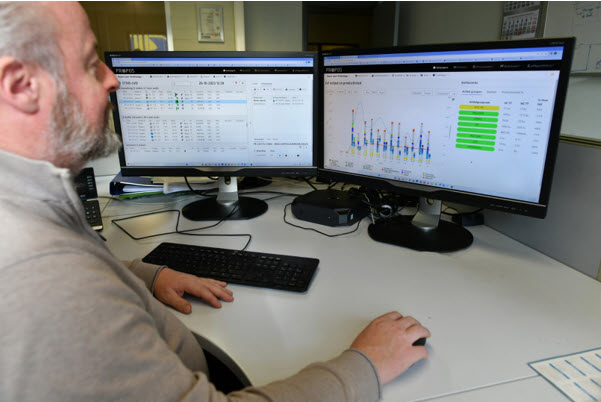
Voorbeeld van het werken met de gebruikersvriendelijke analysemodule van PROPOS.
Waar we in PROPOS over ‘productiecellen’ of ‘cellen’ praten, kun je dat het beste vertalen naar ‘afdelingen’. Met OTD bedoelen we on time delivery, dus leveringsbetrouwbaarheid.
Om OTD richting je klanten te verbeteren, is het goed om te weten hoe betrouwbaar de diverse onderdelen van productie aan elkaar leveren, de interne OTD. Want waar dat het minst goed is, wil je als eerste verbeteren. Naast de OTD van de fabriek als geheel, kun je daarom in PROPOS heel gemakkelijk de OTD gegevens per productiecel opvragen. Daarbij geeft PROPOS al direct aan welke productiecellen goed of minder goed presteren. Maar daarmee is nog niet direct alles gezegd. Want een bepaalde productiecel die een slechte interne OTD heeft, kan daar misschien niet eens wat aan doen. En wat is de oorzaak van die slechte prestatie? Daarom geeft de PROPOS cel-OTD analyse meerdere waardes (grafieklijnen) per productiecel. Allereerst zal ik twee van die waardes behandelen: OTD%-uit en OTD%-in. Op basis daarvan is ruwweg een drietal scenario’s mogelijk voor een productiecel die meer inzichten bieden dan je in eerste instantie zou verwachten. Die scenario’s zal ik hieronder uitwerken. Daarna zal ik nog een derde analysewaarde die in PROPOS beschikbaar is bespreken. Deze geeft een aanwijzing voor de mogelijke oorzaak van een minder goede cel-OTD prestatie.
Bekijk onderstaande grafiek voor een bepaalde productiecel voor een bepaalde periode. De blauwe lijn geeft aan hoeveel procent van de orders de cel op tijd heeft verlaten. Dat is met zo’n 55-60% aan de lage kant. De oranje lijn geeft aan hoeveel procent van de orders op tijd zijn gearriveerd in deze cel, dus op tijd zijn toegeleverd door voorgaande cellen. Dat percentage is ligt ook rond die 55-60%. De OTD-uit loopt mee met de OTD-in. Dat betekent dat deze cel weliswaar een slechte OTD score heeft maar de oorzaak ligt bij de toelevering. Daar dienen we ons eerst op te richten.
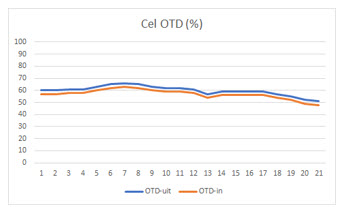
Scenario 1. Slechte OTD voor de productiecel maar deze cel is niet de oorzaak want toelevering is slecht. Geen directe actie vereist voor deze cel.
Voor het volgende scenario bekijk je de grafiek hieronder. De productiecel heeft een slechte OTD, wederom zo rond de 55-60%. De toelevering is echter een stuk beter. Dat betekent dat deze productiecel wel degelijk een negatieve bijdrage levert aan de totale OTD en het de moeite waard is hier met de betreffende mensen een verbeterproject te starten.
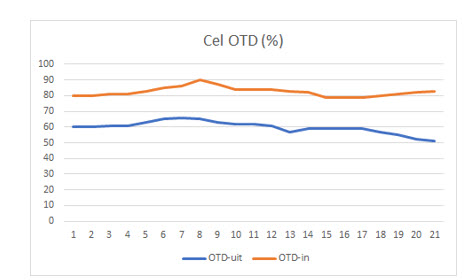
Scenario 2. Slechte OTD voor de productiecel en deze cel zorgt voor een lagere OTD. Actie vereist.
Het volgende scenario toont de omgekeerde situatie. De OTD-uit is een stuk hoger dan de OTD-in. Dat betekent dat deze cel problemen van voorgaande cellen oplost! Qua OTD hoeven we hier dus niet direct actie op te ondernemen. Echter, we kunnen hier wel andere interessante informatie uit afleiden. Dat de cel een slechtere OTD goedmaakt, kan betekenen dat de voorgecalculeerde wachttijden of voorgecalculeerde productietijden wel eens aan de hoge kant kunnen zijn. Dat biedt mogelijkheden voor doorlooptijdverkorting of het verlagen van de voorgecalculeerde kosten. En ook die zaken bieden concurrentievoordeel.
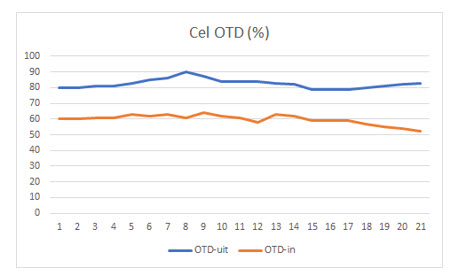
Scenario 3. Productiecel verbetert interne OTD. Ook uit dit inzicht is concurrentievoordeel te behalen.
Naast de twee waardes OTD-uit en OTD-in biedt deze PROPOS analyse nog een derde waarde, een derde lijn in de grafiek. Dat is het percentage orders dat binnen de voorgecalculeerde bewerkingsdoorlooptijd kon worden afgewerkt. De bewerkingsdoorlooptijd is de tijd tussen het moment dat een order in een productiecel voor het eerst wordt gestart tot het moment dat die volledig klaar is. Deze tijd noemen we in PROPOS de TT-DLT (touch time doorlooptijd). Deze lijn geeft een indicatie van de oorzaak van een slechte of goede OTD. Als de OTD van een cel laag is en het TT-DLT percentage is ook laag, dan zijn orders telkens te lang in bewerking. De oorzaak van de problemen kun je dan in eerste instantie zoeken in de uitvoering van de werkzaamheden. Misschien is de voorcalculatie telkens te laag. Of misschien loopt men bij de uitvoering telkens tegen problemen aan zoals fouten op tekeningen of machinestoringen. Omgekeerd, is de OTD van een cel laag en is het TT-DLT percentage hoog, dan ligt de oorzaak eerder in het feit dat orders te lang liggen te wachten voordat ze in bewerking worden genomen. De productiecel zal dan wellicht een bottleneck zijn – hetgeen uit andere analyses in PROPOS ook zal blijken – en het loont de moeite om (flexibele) capaciteit op te gaan schalen. Bekijk onderstaande grafiek. In dit voorbeeld is de OTD van de cel relatief slecht maar ook de TT-DLT is relatief slecht met rond de 50%. De kans is groot dat de hoeveelheid werk telkens tegenvalt ten opzichte van de voorcalculatie of dat er telkens veel onduidelijkheden tijdens de uitvoering zijn.
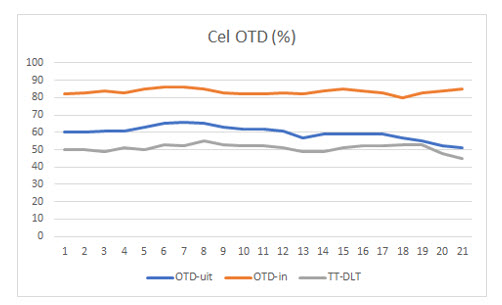
Samengevat is de PROPOS cel-OTD één van de vele gebruikersvriendelijke analyses die waardevolle inzichten geeft om je productieproces te verbeteren. Het geeft aan welke onderdelen van productie aandacht nodig hebben om de komende periode tot betere prestaties te komen. Daarnaast krijg je een idee over de richting waarin moet zoeken voor optimalisaties. Als bonus krijg je informatie over dingen die beter lopen dan verwacht, waarmee je ook je voordeel kunt doen.
In een van de volgende posts zal ik wat meer aandacht besteden aan de dagelijkse praktijk van het
werken met PROPOS. Want juist ook voor die dagelijkse praktijk biedt PROPOS tal van tools en
inzichten om een optimale flow van orders te bereiken.